Press brake tooling, often overlooked but indispensable in metal fabrication, plays a pivotal role in the precision bending of sheet metal. From shaping everyday items to manufacturing critical components for industries, press brake tooling serves as the linchpin of efficient metalworking. In this article, we delve into the vital reasons why press brake tooling is crucial for achieving quality, accuracy, and versatility in metal bending processes.
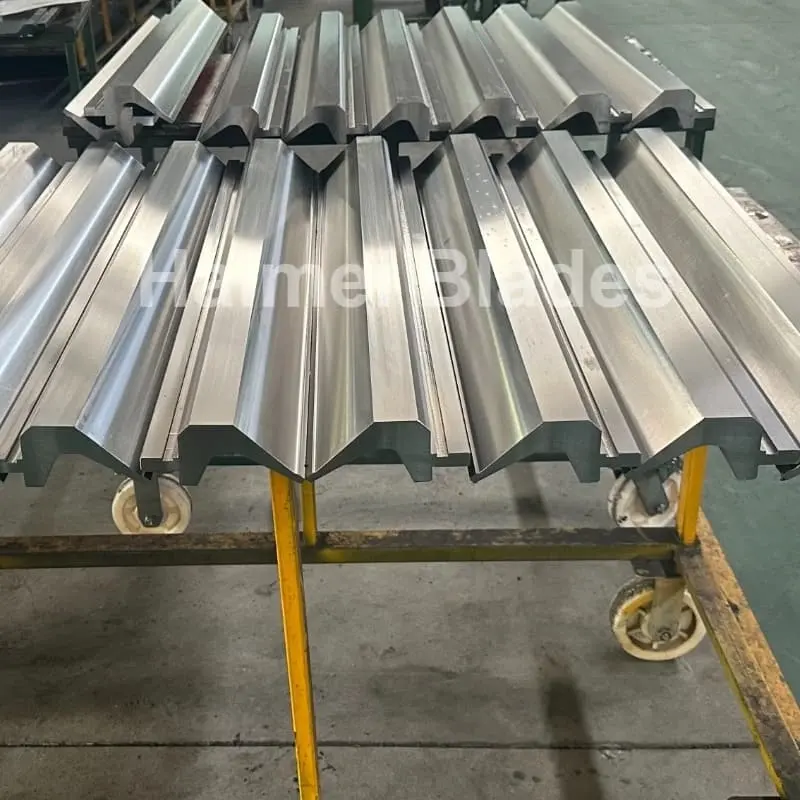
Precision and Accuracy
At the heart of press brake operations lies the quest for precision. High-quality tooling ensures that each bend meets exact specifications, crucial for maintaining consistency across production batches. This precision minimizes errors, reduces waste, and enhances overall product quality.
Versatility
The ability to handle a wide range of bending angles, shapes, and sizes is a hallmark of advanced press brake tooling. This versatility allows manufacturers to respond swiftly to diverse design requirements without the need for multiple setups or machinery changes. It promotes flexibility in production planning and supports agile manufacturing practices.
Efficiency
Time is money in manufacturing. Efficient press brake tooling setups streamline production processes by reducing setup times and increasing throughput rates. This not only boosts productivity but also optimizes resource utilization and lowers operational costs per part. Enhanced efficiency translates directly into improved competitiveness in the market.
Durability and Longevity
Robust tooling materials and designs are essential for withstanding the rigorous demands of metal bending. Durable tooling minimizes downtime due to wear and tear, ensuring continuous operation with fewer interruptions for maintenance or replacement. Longevity in tooling contributes significantly to overall equipment reliability and cost-effectiveness.
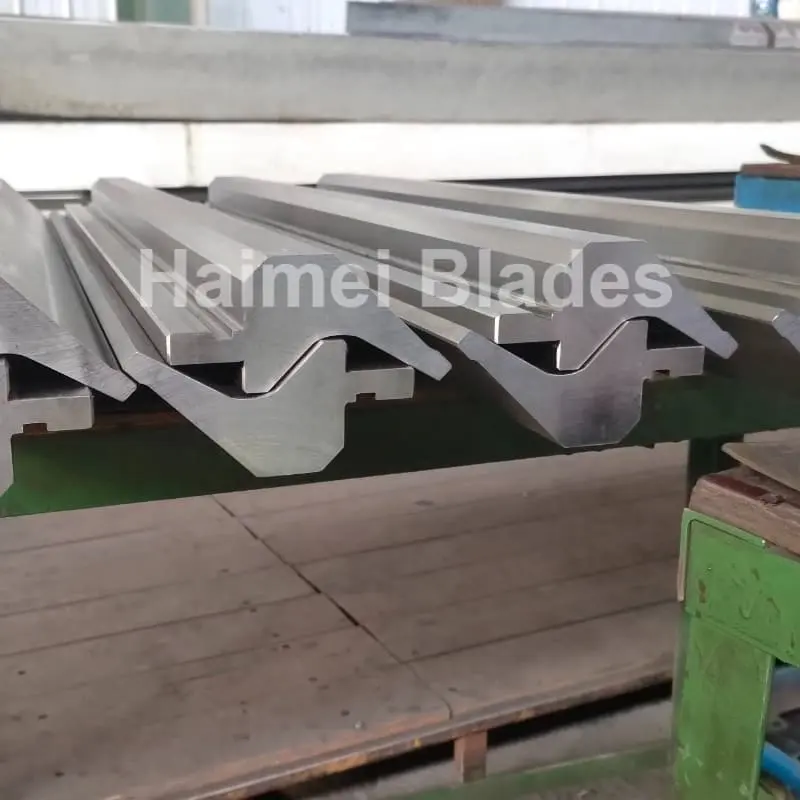
Safety
Workplace safety is non-negotiable. Well-engineered press brake tooling incorporates safety features such as ergonomic designs, protective coatings, and intuitive operation interfaces. These elements reduce the risk of accidents during setup, operation, and maintenance, fostering a secure working environment for operators and technicians alike.
Consistency in Quality
Consistent tooling performance translates directly into consistent part quality. Manufacturers can rely on uniform bends, shapes, and dimensions, meeting stringent customer specifications and quality standards consistently. This reliability builds trust with customers and strengthens brand reputation over time.
Innovation and Customization
Advanced press brake tooling technologies empower manufacturers to innovate in bending techniques and customize products to meet unique market demands. From complex geometries to specialized finishes, modern tooling capabilities facilitate creativity and differentiation in product offerings, driving market leadership and customer satisfaction.
Cost-Effectiveness
While the initial investment in high-quality tooling may appear substantial, the long-term cost-effectiveness is undeniable. Reduced scrap rates, minimal rework, and increased operational efficiency contribute to significant cost savings over the equipment’s lifecycle. Smart investment in tooling pays dividends in terms of profitability and sustainable growth.
Adaptability to Material Variations
Press brake tooling is engineered to accommodate a wide range of material types and thicknesses, from mild steel to aluminum and stainless steel. The ability to adapt to different material properties and geometries makes press brake tooling an essential asset for tackling diverse fabrication projects, from prototype development to large-scale production runs.
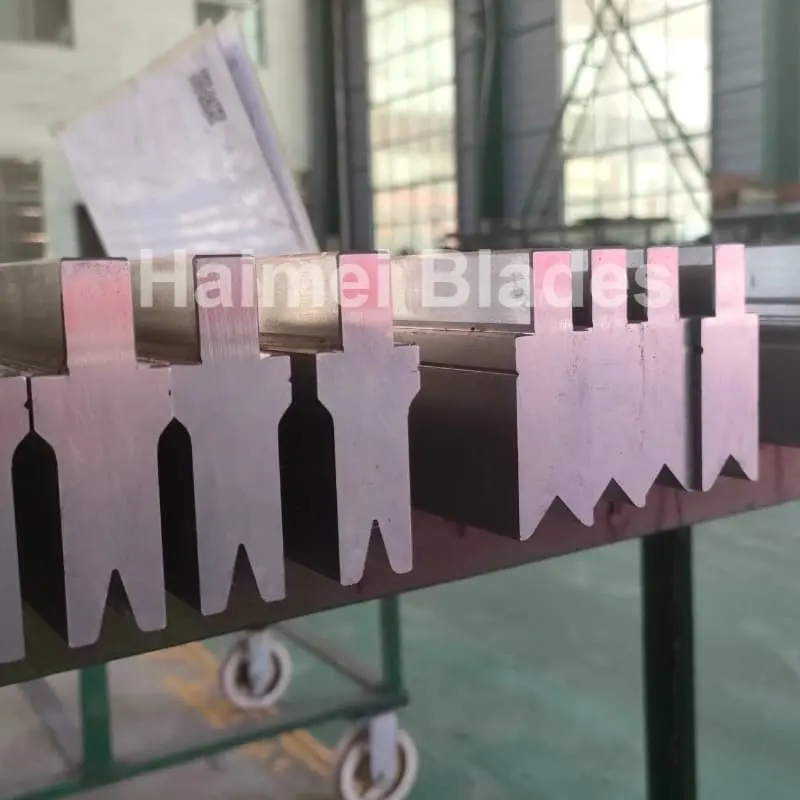
Competitive Edge
Equipped with state-of-the-art press brake tooling, manufacturers gain a competitive edge in delivering superior product quality, faster turnaround times, and enhanced design flexibility. This capability is crucial in meeting evolving market demands and securing a leadership position in the dynamic manufacturing landscape.
In conclusion, press brake tooling transcends its role as mere equipment components to become foundational pillars of efficiency, quality assurance, and innovation in metal fabrication. Investing in advanced tooling technologies not only elevates operational performance but also positions manufacturers to excel in an increasingly competitive global marketplace. By prioritizing the right tooling solutions, businesses can forge ahead with confidence, meeting customer expectations while driving sustainable growth and profitability.