Industrial circular slitter blades are indispensable tools in various manufacturing processes, serving critical roles in cutting and converting materials like paper, film, foil, textiles, and non-woven fabrics. The selection of materials for these blades is pivotal to ensure efficiency, durability, and precision in cutting operations. In this comprehensive article, we delve into the diverse materials commonly utilized in manufacturing industrial circular slitter blades, exploring their unique properties, advantages, and applications.
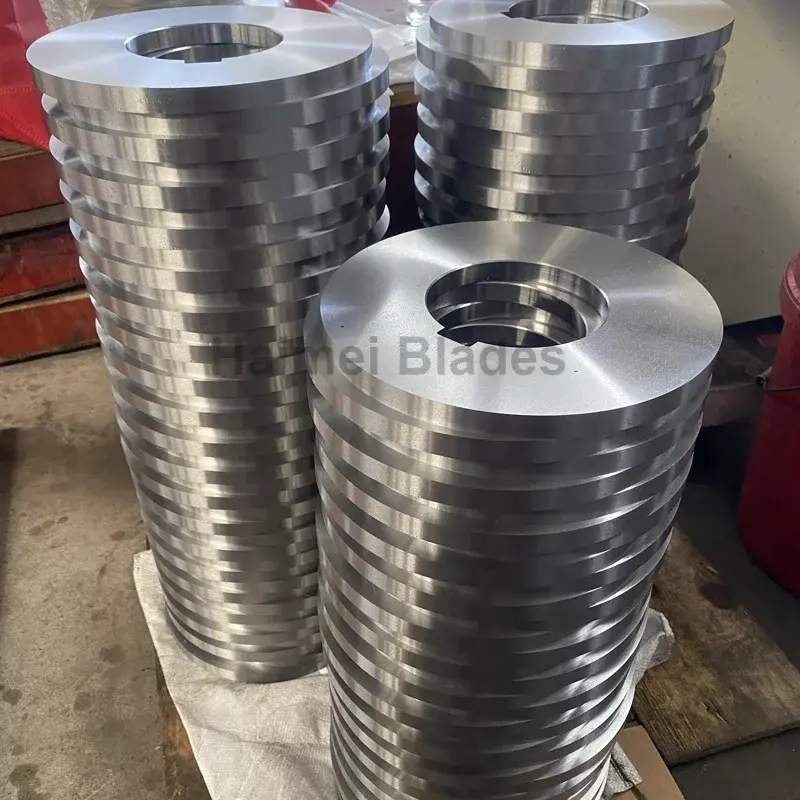
High-Speed Steel (HSS):
High-speed steel (HSS) stands as one of the most prevalent choices for industrial circular slitter blades. Renowned for its exceptional wear resistance, hardness, and ability to maintain sharp cutting edges even under high temperatures, HSS blades offer versatility across a broad spectrum of materials. This includes paper, plastics, and metals. Notably, HSS blades exhibit robust toughness, enabling them to withstand the demanding rigors of high-speed cutting processes without compromising on performance.
Tungsten Carbide (WC):
Tungsten carbide emerges as a material of choice for applications demanding exceptional hardness and wear resistance. Circular slitter blades crafted from tungsten carbide demonstrate remarkable durability, retaining sharp edges for extended durations. This results in prolonged blade life and reduced downtime for sharpening or replacement. Particularly suited for cutting abrasive materials like fiberglass, carbon fiber, and composites, tungsten carbide blades excel in challenging cutting environments.
Ceramics:
Ceramic circular slitter blades are gaining prominence in industries requiring superior wear resistance and cutting precision. These blades are fashioned from advanced ceramic materials such as zirconia or alumina, renowned for their exceptional hardness, chemical inertness, and resistance to wear and heat. Ceramic blades find application in high-precision cutting tasks, notably in electronics manufacturing and semiconductor production, where clean, precise cuts are imperative for optimal performance.
Diamond Coatings:
Some industrial circular slitter blades incorporate diamond coatings to elevate their cutting prowess and longevity. Diamond coatings confer extreme hardness and abrasion resistance to the blades, enabling them to effortlessly cut through tough materials while retaining sharpness over prolonged use. Widely used in cutting applications involving highly abrasive materials like glass, ceramics, and hard metals, diamond-coated blades exemplify durability and reliability in demanding cutting environments.
Carbide-Tipped:
Circular slitter blades featuring carbide tips combine the toughness of steel with the hardness of carbide to deliver superior cutting performance. These blades boast a steel body with carbide inserts or tips brazed onto the cutting edges. Carbide-tipped blades offer exceptional wear resistance and cutting precision, making them well-suited for demanding applications such as cutting corrugated cardboard, rubber, and textiles. Their versatility makes them a preferred choice across various industries.
In conclusion, industrial circular slitter blades are manufactured using a diverse array of materials, each chosen for its unique combination of properties tailored to specific cutting applications. Whether it's high-speed steel for general-purpose cutting, tungsten carbide for abrasive materials, ceramics for high-precision tasks, diamond coatings for extreme durability, or carbide-tipped blades for versatile performance, manufacturers have an extensive range of options to meet the diverse needs of modern manufacturing processes.
Choosing the right material for circular slitter blades is paramount to achieving optimal cutting performance, maximizing productivity, and ensuring the quality of finished products. With continual advancements in material science and manufacturing technologies, the future holds exciting prospects for further enhancing the capabilities and performance of industrial circular slitter blades.