In the fast-paced world of industrial manufacturing, where precision, durability, and efficiency are non-negotiable, polyurethane slitting spacers emerge as indispensable components. These specialized spacers not only facilitate seamless operations but also contribute significantly to improving product quality and reducing downtime across various industrial sectors. Let's explore in detail the substantial benefits of integrating polyurethane slitting spacers into industrial applications.
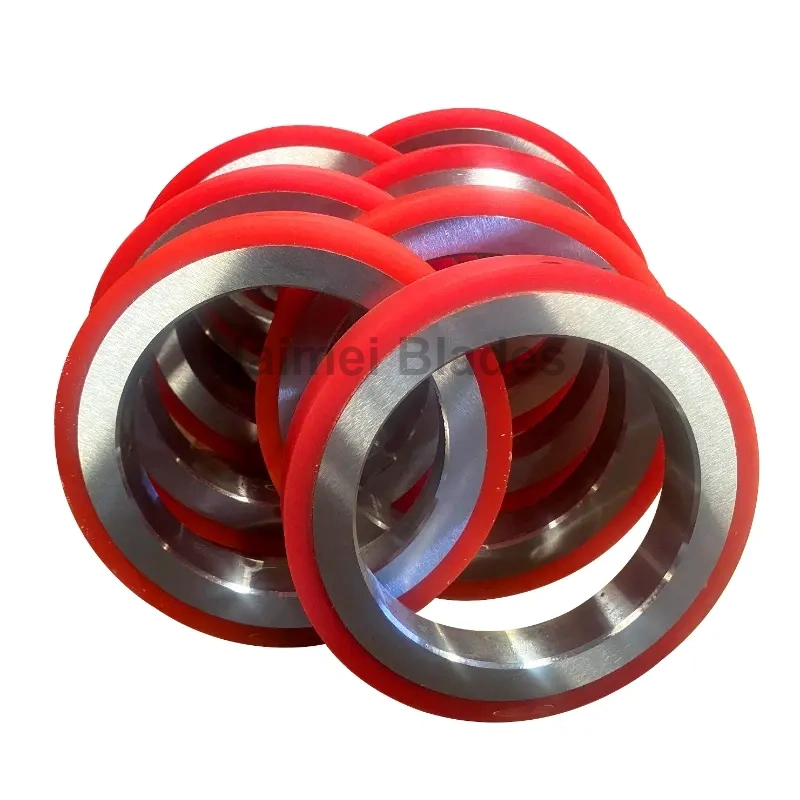
Precision Engineering for Consistent Performance
Polyurethane slitting spacers are meticulously engineered to ensure precise alignment and consistent performance in critical industrial processes:
Blade Positioning: In sectors like paper converting and flexible packaging, polyurethane spacers maintain exact blade positioning during slitting operations. This precision guarantees uniform slitting widths, crucial for meeting stringent quality standards and minimizing material waste.
Dimensional Stability: The inherent dimensional stability of polyurethane helps maintain tight tolerances over extended periods of use. This stability is vital for applications requiring precise cuts and consistent product dimensions, ensuring every output meets exact specifications.
Durability Under Demanding Conditions
Industrial environments demand robust solutions capable of withstanding harsh conditions and intensive use. Polyurethane slitting spacers excel in durability and resilience:
Abrasion Resistance: Polyurethane's exceptional resistance to abrasion ensures prolonged spacer lifespan even in high-speed slitting applications. This resistance minimizes wear on blades and other components, reducing maintenance frequency and operational disruptions.
Chemical Compatibility: They exhibit resilience against oils, solvents, and chemicals encountered in industrial settings, maintaining performance integrity and longevity despite exposure to corrosive substances.
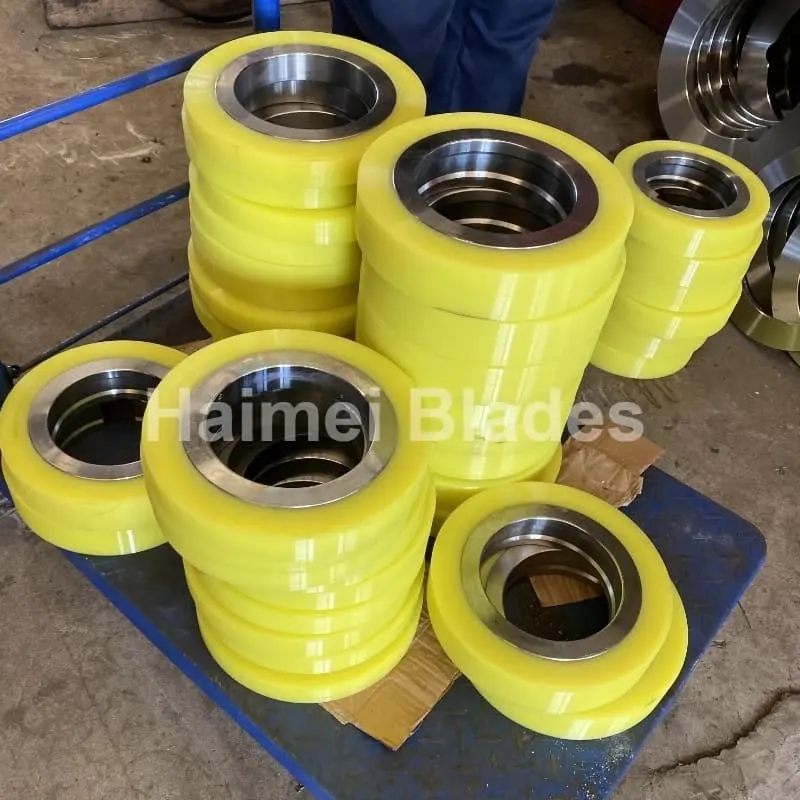
Friction Reduction for Enhanced Efficiency
Reducing friction is essential for optimizing operational efficiency and extending equipment lifespan. Polyurethane slitting spacers offer significant advantages in friction management:
Low Friction Coefficient: Their smooth surface and low coefficient of friction reduce wear on moving parts, such as blades and shafts, thereby lowering energy consumption and operational costs associated with maintenance and replacement.
Noise Dampening: Polyurethane's inherent dampening properties contribute to quieter operation environments, improving workplace conditions and compliance with occupational safety standards.
Operational Agility and Safety Compliance
Achieving operational agility and maintaining safety standards are paramount in modern manufacturing facilities:
Quick Installation and Adjustment: Polyurethane spacers facilitate swift setup and adjustment of slitting equipment, minimizing downtime between production runs and enabling rapid response to production schedule changes.
Environmental and Safety Benefits: They are recyclable and environmentally friendly, aligning with sustainable manufacturing practices. Moreover, polyurethane spacers adhere to stringent safety regulations, ensuring operator safety and reducing risks associated with equipment malfunction.
Conclusion
Polyurethane slitting spacers represent a cornerstone of efficiency and reliability in industrial manufacturing. Their ability to ensure precise slitting, withstand demanding conditions, reduce frictional losses, and enhance operational safety underscores their pivotal role in optimizing production processes. As industries continue to evolve towards greater efficiency and sustainability, polyurethane slitting spacers stand out as a proven solution for maximizing productivity, minimizing waste, and achieving consistent quality outputs. By integrating these advanced spacers into industrial operations, businesses can unlock new levels of performance and profitability while contributing to a safer and more sustainable future.